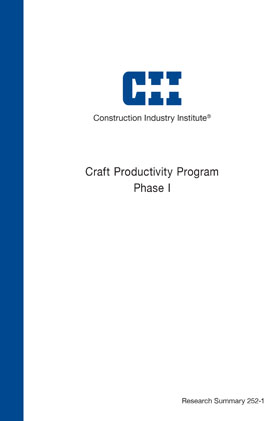
Construction Productivity Program -- Phase I, Version 1.1
Achieving a 50% improvement in construction craft productivity in six years would break a century-old tradition of stagnation interrupted by periodic improvement. This research summary describes the first phase of a six-year research program tasked with just that challenge to tradition. Central to this program is a focus on craft worker productivity and its relationship to best practice use.
Direct work typically amounts to no more than 35-45% of a craft worker’s time on the job. Improving craft productivity requires improving direct work time. To increase direct work time, the availability of materials, information, and tools at the workface have to be improved. There will be no “magic bullet” that will make this happen, but rather a series of innovations that together produce change. They will include a combination of broad improvements in practice and focused improvements in technology and process.
To help the industry realize these improvements, Research Team 252’s (RT 252) five-phase program annually introduces innovations through a research sequence comprised of innovation workshops, field trials, analysis, and implementation tool delivery. Each phase has three parts: (1) analyzing CII Benchmarking & Metrics (BM&M) data to identify potential productivity best practices; (2) exploring opportunities for productivity improvement through craft information, technology support for labor, work packaging/organization, and human behavior; and (3) soliciting innovation input from workshop attendees and team members.
Analysis of BM&M metrics data was focused in the first phase on investigating the relationship between particular field practices and productivity of the mechanical trades. Significant relationships were found between improved productivity and best practices in materials management, safety, team building, front end planning, and automation and integration. These practices, however, are not additive; they are highly correlated and interdependent. Projects that were advanced implementers of these practices experienced as much as a 50% average productivity advantage over projects that were weak implementers. Clearly, implementing these best productivity practices can make all the difference between a weak and a strong performer. But, it is natural to ask whether CII’s BM&M database includes all the best practices or primarily those for which CII has produced products, and whether relatively conventional best practices exist with similar impact.
Thus, RT 252’s efforts in the first research phase also focused on a thorough search and definition of best productivity practices. Once these practices have become rigorously weighted and properly structured, they will become part of a Best Productivity Practices Implementation Index (BPPII). The BPPII will be thoroughly validated in Phases II and III, and will be delivered as an implementation tool in the final phase of the program. No existing CII tool addresses productivity as directly as the BPPII will. Until it is fully developed, however, exciting innovations will continue to emerge and this research program will continue to track them.
For this phase of the program, emerging productivity improvement innovations for the mechanical trades were identified by the team and prioritized. Thorough analysis, including field data analysis, was conducted on each innovation in a structure that includes: (1) the problem addressed; (2) the definition of the innovation in terms of technology, process, and organizational change; (3) the analysis of field data and risks associated with implementing the innovation; and (4) the guidelines for implementation. Six significant innovations are delivered: (1) weld-less and modularized pipe supports, (2) laser scanning, (3) quick connect structural steel pipe supports, (4) cut-length elimination on modules, (5) innovative scaffolding systems, and (6) weld-less pipe joining. While these innovations are focused primarily on the mechanical trades, innovations in Phase II are expected to be more cross-cutting, including craft training and work planning innovations.
Implementing the best productivity practices identified in this first phase, as well as the innovations listed above, is expected to result in significant productivity improvement on any project. More is yet to come in subsequent project phases. This summary is divided into two parts. Part I provides an overview of the Craft Productivity Program. Part II provides the results of Phase I, which focused on mechanical productivity.