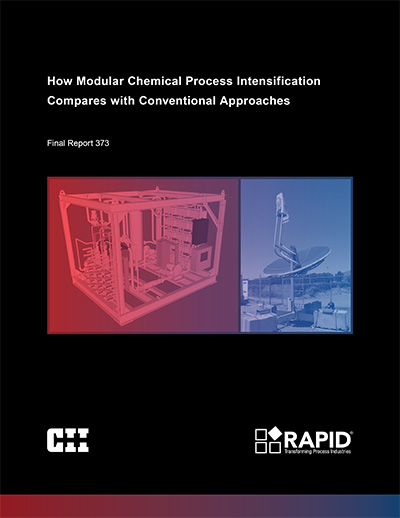
How Modular Chemical Process Intensification Compares with Conventional Approaches
Chemical manufacturers have an opportunity to make a step change by capitalizing on the synergies between chemical process intensification and plant modularization, but businesses are hesitant to depart from conventional methods of plant design and construction to adopt these new approaches. The industry needs to see some proof – economic case studies that can make the business case for process intensification and plant modularization – before stakeholders will be willing to commit to rethinking plant design and act on these new possibilities.
CII and the RAPID Institute collaborated on this study to raise awareness of the benefits and drawbacks of modular chemical process intensification (MCPI). The primary objective of Research Team 373 (RT-373) was to contrast the business case economics of MCPI with the results attained by using conventional stick-built (CSB) approaches to plant construction.
To accomplish this purpose, the team compared the economics of four MCPI case studies against CSB plants that produced the same chemical product at the same production capacity. These case studies used a variety of technologies and the technologies emerged from either manufacturer-operators and developer-suppliers. The team found a range of results, but there was evidence that some of these technologies can be very effective for the companies that use them, enabling the following benefits:
- Drastic reduction in plant volume and footprint
- Up to 87% less CAPEX and up to 14% less OPEX
- A fifth of the payback period
- Nearly twice the net present value
Specifically, RT-373 identified MCPI case studies that reduced CAPEX through a sizeable reduction in plant footprint, which led to less work scope for interconnecting systems. Further, the team identified cases where OPEX was reduced in MCPI plants due to a reduced requirement in operating staffing or from a reduced number of operating steps.
This study also examined decision drivers – the benefits and drawbacks that participants perceived would most significantly affect the comparative economics of these projects. The team gathered these decision drivers from previous academic research and case study participants identified the most important decision drivers. Process safety, cost savings, energy savings, and reduced environmental impacts are MCPI decision drivers that were commonly considered to be benefits of MCPI. However, while MCPI can have many benefits, the case studies also revealed that some novel process intensification equipment is still under development and can be more costly and energy-intensive than its CSB equivalent.
As Figure 1 shows, for Case Study 1, the MCPI plant’s spatial volume was one 250th of a comparable conventional plant (FR-373, p. 17).
Figure 2 captures how MCPI shortened project duration by 70% in Case Study 1 (FR-373, p. 18).
As this portion of Table 3 shows, on Case Study 1 the project CAPEX was reduced by 87% (FR-373, p. 19).