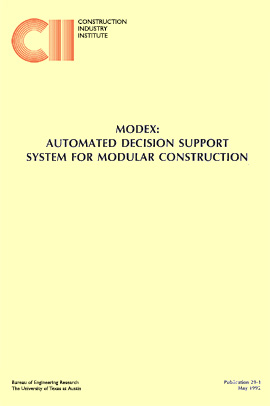
MODEX: Automated Decision Support System for Modular Construction
This document is presented as a reference for industry professionals to examine the feasibility of modularization. The purpose of this document is to introduce a decision support system that enables the user to perform an initial feasibility study on the use of modular construction.
The motivation for this research is threefold:
- A lack of documented information about modularization decision support and the need to compile knowledge from experts in the field
- The absence of a systematic process to perform modularization feasibility studies
- The development of a computer-based application tool to aid Engineering and Construction industry professionals and owners in the performance of an initial feasibility study
This summary document introduces a new decision support tool, MODEX (MODularization EXpert). This PC-based program enables owners and engineering and construction (E&C) firms to make preliminary engineering decisions regarding the use of a modular appproach to plant design and construction during early planning and conceptual design phases. Based on inital feedback from E&C decision makers, MODEX can determine if the use of a modular design can contribute to significant cost savings in facility construction and operation.
- Safety – by removing dangerous work hours from the field (i.e., through less work at height)
- Reduction of construction time – if economies can be found through speed of fabrication
- Reduced labor costs – by moving hours off-site to a less expensive location
- Labor availability – if there is a shortage at the construction location
- Weather – by moving work away from the field and into a climate controlled/friendly location
- Quality – by moving work to factory conditions
- Reducing interruptions to operating plant – by moving work that would be performed at the operating site to off-site
- Transportation costs – increased cost of handling large shipments, both off-site and in terms of offloading and setting costs on-site
- Transport size/accessibility limitations – logistics such as roadway weight limits restrict efficiency gains from large modules
- Increased engineering effort – there are more up-front engineering costs and need for
The interviews with modularization experts provided an extensive amount of information about the modularization feasibility study process. The most important discovery was the delineation of 5 factors to consider when a study is performed, that include:
- Plant Location
- Labor Considerations
- Plant Characteristics
- Environmental and Organizational Factors
- Project Risks