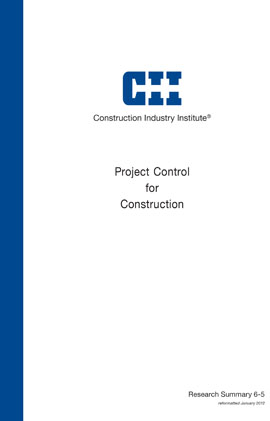
Project Control for Construction
The potential for the success of a construction project is largely dependent upon the quality of the project controls system and staff assigned because that function is really the eyes and ears of management. Lacking this function or operating with a substandard system is equivalent to operating in the blind.
Project controls is concerned with cost, schedule, and materials control. These areas are extremely interrelated, and therefore the system must be designed to assure full accountability for their interrelationships. As is so often stated, there must be integrated project control.
Cost control is not cost accounting. The Cost Breakdown Structure provides the basic structure for cost control and establishes the Control Budget; its structure differs significantly from the structure for cost accounting. It is designed to catalog budgeted and actual expenditures for purposes of identifying cost problems, establishing cost trends during the course of the project, and to provide valuable cost data for the planning of future projects. Since the major cost variable on a construction project is labor productivity, a major component of the cost control subsystem is the tracking of work-hours in parallel with quantity tracking.
Schedule control requires the establishment of a Control Schedule at the outset of construction. This is the reference document for schedule planning and is modified only as a result of owner-approved changes. Working Schedules reflect the realities of progress to date and the plan for the short term. In all cases, the Working Schedules should be planned to keep the project as close to the Control Schedule as possible. The design of schedules should be such that they are realistic and a positive planning tool. Control Schedules which are too detailed soon lose their usefulness because they invariably contain arbitrary or false logic and field personnel no longer have confidence in them. A sure sign of schedule planning failure occurs when project control engineers can be found spending all their time updating schedules while the field personnel are planning their work as best they know how and simply reporting the results.
Materials control is one of the included functions of a Materials Management Program. Since materials deliveries directly affect the ability to schedule work, materials tracking should be a subsystem within the project controls system and tied to the scheduling system. The source of materials tracking information will come from procurement and expediting personnel, and positive coordination and cooperation with those personnel must be established and maintained throughout the project’s life.
The Project Controls Section must be staffed by personnel knowledgeable about field operations. It should not be treated as an accounting or data processing activity, and should report directly to the field project manager. It should not share a computer system with another function if that sharing in any way denies the availability of the computer or printers to project controls. The project control engineers must be able to access databases and prepare reports for management at all times and on short notice.
Finally, the system must be designed to meet specific contractual requirements plus the traditional needs of the contracting parties.