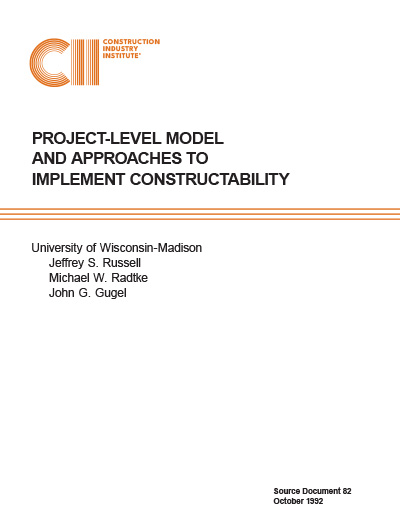
Project-Level Model and Approaches to Implement Constructability
Implementing construction knowledge during the design of a project can be an effective tool in achieving project success in regards to cost and schedule. A constructability program that strives to create an interdependence between the designer and contractor at all phases of the facility delivery process while also recognizing schedule constraints and new construction technologies could produce benefits well beyond the cost of the additional effort.
However, many problems stand in the way of creating a constructability program. Oftentimes, projects are conceived with the construction phase completely separate from the rest of the facility delivery process. The possible benefits are many times ignored because they may be difficult to quantify in order to justify the cost of the program. Also, various ideas regarding the scope of constructability among the construction industry can create misconceptions about the extent of the benefits.
Research Objectives and Scope
The goal of this investigation is to better understand the procedures contained in constructability programs implemented on projects. Specifically, constructability aspects present during the conceptual planning, design, procurement, and construction phases of the facility delivery process are addressed. The first step towards this goal is identifying and analyzing constructability practices already present in the construction industry. The next step is developing model project-level implementation procedures to assist organizations in developing formal constructability programs.
Research Methodology
This investigation was conducted in five steps. First, research participants reviewed literature provided mostly by the original CII Constructability Task Force. Next, usable data regarding existing constructability programs of 262 organizations was collected by means of a questionnaire survey. Chapter 3 focuses on the specifics of this questionnaire. The participants then conducted interviews gathering usable information from 62 organizations. Chapters 4 and 5 discuss further the interview procedure. With the information gathered, model constructability implementation procedures were developed and, as the final step, subjected to criticism by four selected organizations. Comments from these organizations led to further modification of the model.
Current Industry Constructability Programs
The level of a constructability program, if any, within an organization depends on their perception of the breadth of the program. Information collected through questionnaires and interviews show these perceptions can range from design reviews just prior to release of construction documents to formal constructability programs with extensive documentation of costs and benefits. This shows that while many organizations may feel they are implementing constructability, in fact their efforts are to late in the facility delivery process to achieve significant benefits. From the 262 usable questionnaires returned, 22% indicated that they have a formal constructability program, 46% reported informal constructability procedures, and 32% reported no constructability procedures at all. Of the organizations claiming informal practices, several indicated that these practices were only applied during the construction phase. In these situations, construction knowledge was not applied during the design but rather the re-design once the project is under way. On average, projects using a formal constructability program resulted in a an estimated 5.7% savings in project cost due to reduced capital construction cost, reduced protect duration, better safety, and quality performance.
Interview data revealed eight general approaches to constructability currently used in the construction industry. These approaches are not a measure of the effectiveness of constructability but rather indicate the level of distinction of constructability programs from other project management activities. Each approach depends on the variety, type, and size of projects in which an organization participates. The various approaches to constructability are presented below:
Construction Management Historical Practice – No distinction between constructability and “good construction management practices” is made. Constructability input is often obtained by in-house personnel. Very little documentation for constructability is provided including within contract documents. This approach lacks any method of estimating the value of constructability efforts.
Constructability Contract Documents – As in the previous approach, constructability is considered to be an integral part of construction management activities. However, contract clauses and brief constructability procedures are implemented as a part of an informal means of obtaining construction knowledge during the detailed design phase. Some organizations use constructability plan review checklists in order to draw attention to design materials frequently overlooked. This approach addresses the need for an awareness of constructability issues although is again lacks the means to estimate the value of benefits attained.
Constructability Services – Constructability input is considered to be a service provided along with preconstruction services. This approach usually associates constructability input with value engineering. The service usually reviews the costs of design alternatives. Professional construction management organizations often use this approach when involved in the general building or public sector.
Constructability Design Review – Reviews of project design and specifications are performed at set percentages of design completion using formal design checklists. The reviews typically check designs for accuracy, completeness, cost effectiveness, and compatibility with project constraints. Although suggestions during design review are often useful, they necessitate design rework instead of implementing a proactive approach to design. This may also lead to adversarial relationships between design personnel and the review organization. Also, input is usually limited to the owner’s personnel since the contractor typically is not yet selected.
Quality Improvement Program – This involves constructability included as a part of another formal program, typically oriented towards quality. The extent constructability is emphasized varies within this approach from no direct reference to constructability to efforts to track constructability items and their savings. It is difficult, however, to isolate constructability benefits and efforts within such a system.
Specialized Formal Constructability Programs – This approach can be considered involving project-level constructability programs. Such programs obtain constructability input during conceptual planning and preliminary design, establish a philosophy for projects, outline constructability procedures, and track progress of constructability efforts. These programs are usually limited to specific projects and so do not involve formal tracking of lessons-learned or corporate constructability training.
Standard Constructability Guidelines – Organizations that often use formal constructability programs usually incorporate constructability philosophy proven during various projects into corporate constructability manual and training program. As the corporate-level program evolves, the philosophy becomes widely accepted and tracking of constructability savings becomes less necessary. No formalized program for communicating lessons-learned from past projects is created.
Comprehensive Tracking – Similar to the Standard Constructability Guidelines Approach with two additions. First, a paper or computer database is created with the purpose of communicating lessons-learned from project to project. This enables project participants to view construction alternatives and their associated costs and relate it to their own projects. The second feature is a database established to record and track constructability savings, including cost and schedule, in order to justify future use of constructability programs. This approach usually requires a constructability database manager.
Of the eight approaches listed above, the approach adopted by an organization depends considerably on the type of organization. Interviewees included in the investigation were (1) design/contractors, (2) contractors, (3) designers (with CM staff), (4) professional construction managers, (5) industrial owners, (6) manufacturing owners, (7) utility owners, and (8) public sector owners. Only through the application and measurement on individual projects can an organization determine the success of their constructability program. From the 62 organizations interviewed, research participants gathered information detailing constructability programs of 55 different projects. From these projects, four classifications of project-level constructability programs were determined: (1) Formal project-level constructability program, (2) Formal post-facto constructability review, (3) Informal application of constructability, and (4) Untimely constructability input. Only the formal project-level constructability program provided significant documentation to determine its impact on the project. Interview data showed direct links between corporate-level and project-level constructability programs. Chapter 5 displays these links as well as factors influencing project-level constructability approaches. However, note that, as mentioned earlier, the approach to a corporate-level constructability program depends on organization type while the project-level program is the same whether the participant is the owner, designer, or contractor of the project.
Model Constructability Implementation Procedures
Adopting a formal set of constructability procedures is a means to (1) convey an organization’s commitment to constructability and (2) ensure specific constructability activities are conducted when most appropriate on the project. Chapter 6 presents a set of model procedures for a project’s formal constructability program. The entire process is oriented towards owners involved in construction projects. Professional construction management firms, designers, and contractors can adopt portions of the procedures as applicable.
Obtain Constructability Capabilities – The owner should assess available in-house personnel and consider procurement of external design and construction knowledge and experience. This process consists of four steps: (1) assemble key owner team members, (2) define constructability objectives and measures, (3) select project contracting strategy, and (4) secure contractors, vendors, and consultants.
Plan Constructability Implementation – Constructability planning is critical to program success and should begin as soon as possible. Effective planning should include the major project participants to the maximum extent possible. It is suggested that the developed plan be integrated within the project execution plan. Integration of constructability input into execution plans is highly dependent on the project type and contracting strategy. The owner’s project manager should be responsible for providing adequate construction involvement during development of the execution plans. Steps involved within this milestone include: (1) develop constructability team, (2) identify and address project barriers, (3) consult applications matrix and lessons learned, and (4) develop constructability procedures and integrate into project activities.
Implement Constructability – With adequate constructability planning, constructability ideas should be integral with the constructability team’s design, construction, and start-up activities. This milestone involves three steps: (1) apply constructability concepts and procedures, (2) monitor and evaluate program effectiveness, and (3) document lessons learned.
Conclusions
The following conclusions can be drawn from the research investigation described in this report:
- Most organizations participating in the construction industry informally integrate construction knowledge and experience in their planning and design activities. Approximately 78% of owners, designers, contractors, and professional construction management firms surveyed have either informal constructability programs or none at all. Without formal constructability programs, these organizations usually have difficulty: (1) consistently applying constructability concepts on projects, (2) estimating the cost effectiveness of early involvement of construction personnel, (3) generating, storing, and efficiently retrieving constructability lessons learned from previous projects, and (4) creating a team environment between designers and contractors. Many owners that do not apply formal constructability programs on projects are unaware of the potential savings that are being lost by unnecessary rework, reduced quality, lower construction productivity, and increased schedule durations.
- The approach an organization takes to implement constructability on their projects is highly dependent on the project type, contract strategy, and variety of projects that the organization constructs. For example, organizations involved in construction of industrial and manufacturing facilities are more likely to use reimbursable construction contracts and implement formal constructability programs. Organizations involved in general building construction are likely to hire a construction manager for “preconstruction services” rather than implement a formal constructability program. Most projects in the public sector involve fixed-price construction contracts competitively bid from completed design documents. Therefore, many public owners periodically conduct constructability reviews prior to the releasee of design documents. Also, the interviews identified that organizations participating on a large variety of project types usually have more difficulty standardizing constructability program procedures.
- Organizations tend to evolve through various constructability approaches before achieving the optimal type of constructability program. Approximately 23% of the organizations interviewed are currently in transition between constructability approaches. Four steps were identified within the evolution of approaches for owners First, owners typically reference constructability in contract documents to obtain construction knowledge during planning and design. Second, at least one “pilot” project is used to: (1) prove constructability benefits and (2) develop constructability procedures. Third, based upon the success of the project(s), constructability procedures are applied across many projects to educate personnel and reap the benefits. Formalized tracking of lessons learned is conducted if the organization participates on similar types of facilities. Fourth, once the constructability program becomes ingrained in the corporate philosophy, tracking of constructability suggestions may become less formal.
- Formal constructability programs, with procedures similar to those presented in Chapter 6, provide three general benefits to organizations. First, enhanced teamwork and communication leads to more cost effective construction on projects. Second, more effective sharing of lessons learned occurs between projects. Third, contractors can use the constructability savings generated as a marketing tool to receive additional construction contracts from owners.
- Owners should take the first step in implementing constructability on projects. The owner s project manager must be fully committed to constructability enhancement for the project. The owner is the driving force behind constructability on the project by: setting project objectives, selecting the contract strategy, selecting which firms will participate, and funding constructability resources during planning and design.
Recommendations
The research investigation has lead to the following recommendations.
- Organizations should first assess their current constructability approach to determine the best means for constructability improvement. Many organizations have the perception that they are already effectively incorporating construction knowledge and experience into planning and design. An organization’s self-assessment can identify areas for improvement. Assessment should include evaluating: in-house constructability resources, sources of constructability input, timing of constructability input, implications of contract strategies used, contractor feedback, and project performance (i.e., scope changes, design errors, field engineering, labor productivity, accident incident rate, among others). As a result of self assessment, an organization should be able to identify with one of the eight approaches described in Chapter 4. The organization can then assess whether the model is appropriate for their organization.
- Organizations should take a proactive approach to constructability on projects. The use of constructability reviews should only be a small part of a constructability program. When constructability reviews are used as the primary means to obtain constructability input, the following undesirable effects may result: (1) designers may become defensive and (2) contractors may be reluctant to offer suggestions. Proactive constructability programs are more likely to involve construction personnel when the ability to influence costs is greater (i.e., during conceptual planning).
- Organizations that have not implemented a formal constructability program, should consider using a project-level constructability program as a “pilot.” The model implementation procedures provided in Chapter 6 were developed for application on such a pilot project. Management personnel may doubt that the benefits of constructability will outweigh the constructability resources expended during planning and design. By testing the pilot project-level program, the organization can identify whether a corporate-level constructability program is feasible.
The ability to influence construction costs over the life of the project is greatest when constructability is introduced early in the project. The influence of constructibility implemented during the construction phase is less significant than when implemented during conceptual design, procurement, or design phases. (SD-82, p. 10)
Constructability can still influence final project cost during field operations. “Innovative construction method” is a term used when referring to construction methods that are not common practice across the industry but can influence costs or schedule. Two examples of the many innovative construction methods found in the research are:
- Innovative sequencing of field tasks
- Innovative temporary facilities supportive of field methods