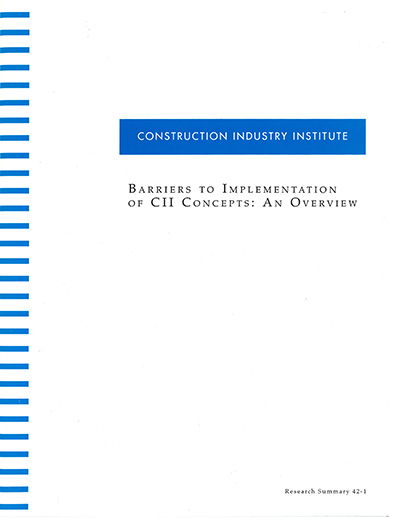
Barriers to Implementation of CII Concepts: An Overview
Are you getting value from your CII membership?
Are the recognized best practices of the construction industry being implemented on your projects?
Are you realizing the potential cost savings and benefits promoted by CII?
By the year 2000:
- 20% reduction in cost and schedule
- 25% reduction in accidents
- 20% improvement in productivity
- 95% predictability of cost & schedule
Does your organization have a commitment (with plans and funding) for:
- a CII Champion in your organization?
- education and training that includes CII recommendations?
- implementation of CII concepts?
Do all appropriate project and construction personnel have access to CII Publications?
If you cannot answer YES to all of these questions, you are not getting the most out of your construction dollars!
Implementation varies by concept and by project. However, implementation in general is not comprehensive in addressing all published recommendations. It is apparent upon analysis that some concepts are not integrated into plans and procedures, and implementation is not consistent with the recommended practices. (RS42-1, p. 13)
Figure 2 shows the results of scoring the project responses as the level of implementation of the concepts. Of interest is the relative ranking of the concepts and the drop off of implementation levels for many of the concepts. The area above the graph indicates the margin for improvement opportunities for each of the concepts.
The barriers to implementation encountered at the project level were common to practically all concepts. A few barriers were found to be concept-specific. To a large degree, the responses indicated an environment of doing the same old thing under increased pressures with “no time to sharpen the saw.” (RS42-1, p. 16)
Barriers to implementation found in industry projects:
- General lack of commitment to the concepts
- Relatively low familiarity of concepts at the project level
- CII materials not being read and utilized at the project level
- Limited emphasis on training and education for implementation of CII recommendations
- Failure to integrate new ideas and recommendations into company procedures
- Limited benchmarking of implementation costs and benefits (no proof of savings)
- Lack of innovative and risk-taking environments
Many of the barriers encountered appeared to follow a pattern from project to project. The most typical barriers fit into the following major categories: (RS42-1, p. 16)
- Management Leadership
- Organizational Culture
- Education
- Measure of Performance
- Communication
Recommendations to achieve higher levels of implementation and realize the benefits of the CII Concepts are provided for Owners, Engineering, and Construction Organizations. Recommendations include: (RS42-1, p. 19)
- Incorporate CII recommendations into company and project plans, procedures, and cultures
- Establish a “champion”
- Provide funding and incentives for implementation
- Promote risk-taking versus punitive environments
- Document the benefits of implementation
- Develop company training that molds CII recommendations to company culture and standard operating procedures
- Provide opportunities for project staff to participate in CII activities
CII recommendations need to be internalized as part of a company’s organizational culture. As with quality, all organizations should have a “champion” or focal point for knowledge, communication, and implementation of CII Concepts. Company management and responsible individuals must provide the commitment and leadership to make the needed changes and improvements happen. In order to invest in future organizational and project performance advantages, the commitment and funding must be provided for: (RS42-1, p. 20)
- Leadership, education and training
- Development of plans and procedures for implementation
- Assessment and implementation of CII concepts on all projects
- Benchmarking of performance results and benefits