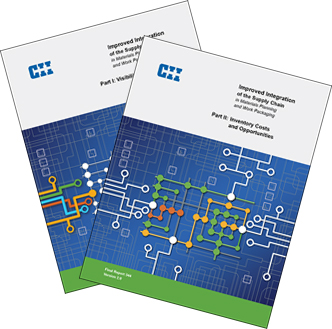
Improved Integration of the Supply Chain in Materials Planning and Work Packaging, Version 2.0
Materials are the life blood of projects. If materials don’t flow smoothly from specification to fabrication to site installation, project performance will be poor. All too often, even well planned and executed projects face disruptions to materials flow. Indeed, late or missing materials are a common occurrence on almost every project.
Part I of this report explored the visibility of materials in the project supply chain and made recommendations to improve materials tracking and support effective decision-making. The volume was based on an initial stage of research that reported on the current state of materials visibility – generally poor – and identified a large number of visibility items and enablers that are associated with common decisions. It concluded that project supply chain performance will improve if projects and firms pay closer attention to visibility.
Version 2.0 introduces Part II, a companion to Part I that explores the opportunities for improvement that may stem from improved visibility. A particular focus of this second phase was to focus on the costs of carrying stocks of materials on the project and, hence, to help teams make better decisions about achieving the right balance of materials as a buffer against the risk of shortages. The researchers see a better understanding of costs as a prerequisite to improving policies or optimizing behavior.
This study presents metrics for excess inventory and a framework for decision-making to augment project planning processes. Collectively, these findings make the case that there are significant opportunities for reducing inventory holding costs while making the material on hand more effective.
A response to the industry survey question, “Would better supply chain visibility materially change how you do business.”
Ten key supply chain activities support tactical- and operational-level decision-making in the detailed design, procurement, and construction phases:
Visibility needed items with detailed definitions at the tactical and operational level across the 10 key supply chain activities requiring decisions for detailed design, procurement, and construction phases.
Average ratings of visibility needed items in terms of ease of access, accuracy, and importance, as rated by RT-344:
- Level or degree of inspection – Assigning critically ratings based on the type of equipment that needs to be inspected (i.e. static equipment, rotating equipment, electrical and instrumentation).
- Review of supplier's quality plan and inspection test package – Confirming alignment to the order expectations.
- Establishment of proper witness points – Ensuring the number of witness Points are in aligned to meeting the committed delivery dates.
- Dissemination of quality performance issues to detailed planners – Timely dissemination of non-conformance reports and similar production issues to appropriate stakeholders (including detailed planners, such as workface planners and senior site supervision) to incorporate known issues into site sequence and inspections plans.
- Information specification in contracts – Contractual definition of desired information and its format to facilitate sharing of supplier design information into project information systems (design tools).
- Data exchange specification and process – Process and definitions for standardized supplier data exchange (i.e., materials handling and design data).
- Establishment of a non-conformance report (NCR) process – Ensuring all non-conformance issues are captured and the proper stakeholders are identified. Have a defined supplier inspection process that enables capturing supply issues at the fabricator as opposed to on site when it may be too late to correct.
Average ratings of enablers in terms of ability to impact project and frequency of competent execution rated by RT-344:
To obtain better insight into the state of inventory on industrial projects, the research team obtained data from 14 sample projects. The researchers found inventory metrics and representations around excess inventory or inventory held longer than plan, and an appendix in Part II shows the inventory levels on each project for recorded materials types in multiple graphical formats.
These metrics can be used with firms’ cost data to calculate specific costs as well as make estimate of holding costs. These metrics are paired with sample representations of the data that are shown to be useful and easily interpreted by project professionals.