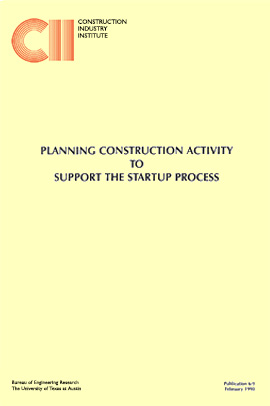
Planning Construction Activity to Support the Startup Process
Owners planning any new facility, particularly one which is a production facility, usually are intent upon that facility being available by a specific date to meet a market goal. Thus, they desire that any activity with the potential to influence that availability be carefully planned and made as efficient as possible. CII Publication 6-3, Model Planning and Controlling System for EPC of Industrial Projects, describes the procedure for optimizing the process. That publication asserts that while facility startup itself must be accomplished in an efficient and orderly sequence, it is equally important that all preceding construction activity be completed in time to support the startup process, and that procurement and engineering be completed to support the construction process.
When speaking of startup, one is referring to startup of systems within the facility. A system is any assemblage of structural, mechanical, electrical, and instrumentation components providing a function or service. Just as a work breakdown structure has many levels, many levels of systems exist within a process or manufacturing facility. In effect, the entire plant is one huge system that is made up of many separate systems and subsystems.
This publication is concerned with the planning of construction to support startup. While some discussion of startup is included to help the reader understand the constructor’s role in the process, major emphasis is on how the constructor converts from a mode which is most cost-effective from a construction viewpoint to one which is most cost-effective from an overall plant viewpoint.
The typical process plant will accomplish startup in stages. Shown below are the typical 6 stages of startup. Manufacturing or power plants will use these stages only to the extent applicable. (RS6-9, p. 4)
Stage 1 – PrecommissioningStage 2 – Commissioning
Stage 3 – Raw Material Introduction
Stage 4 – Operation Testing
Stage 5 – Performance Verification/Acceptance Tests
Stage 6 – Commercial Operation
The overall startup planning process must begin early in the life of the project. The exact timing of long-range systems planning and the timing of a conversion from area to system scheduling will vary from one project to the next. The earlier the planning begins, however, the less potential for startup problems that result in increased costs and delays. Some factors that must be considered to make these decisions are discussed in this publication. (RS6-9, p. 3)
By the 30 percent point of construction, system definition must be communicated to the construction force since it is the basis for detailed startup planning. When construction is about 70-85 percent complete, system completion and precommissioning activities begin, and attention becomes focused on the proper sequencing of bringing entire systems on line.
One point that cannot be emphasized enough is the importance of early planning of the conversion. Planners must be aware that the logic for the entire construction schedule should have its basis in systems startup in spite of the fact that field managers will build by area during most of the project. In their look-ahead planning, the field managers must be continually conscious of the startup logic and the materials managers must continually focus on the need dates of system components by the field.
The first step in defining this organization is the development of a Division of Responsibility Matrix, which catalogs responsibilities during the startup phase. This matrix will show responsibilities for the engineer, constructor, vendor representatives, project personnel, operations personnel, and maintenance personnel. Note an example division of responsibilities matrix for a typical mechanical industrial project is included in the research. (RS6-9, Appendix B, p. 20)
On a fixed-price project, this matrix should be included in the bidding documents or presented in pre-bid discussions. On a reimbursable project, it is advisable that it be available at about the project's 30 percent construction completion point and no later than the 50 percent point.
Operations personnel frequently have significant input in how a plant is started up or restarted. This input will involve the sequencing of the startup of individual systems, the duration of the startup, and any individual system milestone dates to be met.
The Startup Plan should include a detailed checklist and schedule for all activities that must be performed both prior to and during the startup operation. The plan will also include identification of individuals or groups responsible for each activity.
CII Publication 6-3, Model Planning and Controlling System for EPC of Industrial Projects, recommends a “backward” or right to left scheduling approach for an industrial project. The starting point for that effort is the owner’s need date for commercial operation. Working backwards, the sequence and schedule for construction/installation of individual system components can be determined. Thus, startup effectively drives the entire construction schedule as well as supporting procurement and engineering activity. Establishment of system startup dates is an owner function through its engineer and startup team. Development of the construction schedule to support these dates is a contractor responsibility, although it will be done in full coordination with the startup team.
The process has recognized that the ultimate milestone for the project is the owner’s need date and that planning is “backward” from that date. (RS6-9 Appendix C, p. 23)