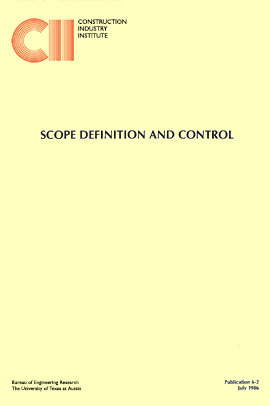
Scope Definition and Control
There has been considerable alarm in the business community over industrial project cost overruns in recent years. What are the causes? The Business Roundtable Construction Industry Cost Effectiveness (CICE) Project Report A-6 states that “Poor scope definition at the estimate (budget) stage and loss of control of project scope rank as the most frequent contributing factors to cost overruns.” A recent report found that some construction industry officials consider lack of scope definition to be the most serious problem on construction projects.
While inadequate definition may be attributable to poor planning and management of projects, it must be assumed that there can be circumstances which either preclude full scoping of projects or force managers to proceed at a level of scope definition less than desirable. Regardless of the reasons, when there is poor scope definition, final project costs can be expected to be higher because of the inevitable changes which disrupt project rhythm, cause rework, increase project time, and lower the productivity and morale of the work force.
Cost overruns on industrial projects can be both apparent and real. Most overruns are calculated by comparing final costs with budgeted costs. If the budgeted costs are not based on a well-defined scope, they are probably low and not a valid base for comparison. Real overruns occur as a consequence of unjustified scope growth during engineering, other engineering changes, and a variety of engineering, procurement, and construction inefficiencies. However, the inescapable conclusion is that scope definition and control is a key factor in both apparent and real cost overruns.
This publication will explore this subject and attempt to answer these questions:
- Why is scope definition a problem?
- Why is scope growth a problem?
- What can industry do to control these problems?
This research describes the various categories of cost estimates that are normally prepared throughout the life cycle of the project. It is recommended that budget estimates should be of the “Control Estimate” category. (RS6-2, p. 4)
Budgets prepared with higher level estimates are subject to high variability and could have the following difficulties:
- Variability for lack of site information
- Pressure exerted on estimators to support rough estimates to produce low cost figures difficult to justify to insure final authorization
- Inability of estimator to predict the direction of design development
- Individual components of an estimate have higher variability than its total
The installation of bulk quantities represents approximately 75% of field labor cost on an industrial project. Therefore it is important that all drawings associated with bulk quantities be completed to get an accurate representation of material and labor cost associated with bulk quantities. (RS6-2, p. 8)
The following two key difficulties should be addressed to improve the process:
- Communication: Standarize on quantity measurement methods used for estimating, statusing, and reporting among all groups within the project
- Design Engineer Involvment: Involve those who generate the quantities in the control process
With a well-defined project, a good project organization, and a good control structure, changes are readily classified and controlled. However, a poorly defined scope does not provide a clear baseline against which changes can be evaluated as being either changes within or outside scope. Regardless of the reason for the change, there is a need for a positive change control system within an engineering organization. (RS6-2, p. 12)
Changes originate from multiple sources including:
- Overlooked items by the engineering team members
- Multiple disciplines working in parallel
- Concurrent engineering
- Safety committee
- Operating and maintenance staff
- Constructability reviewers
- Facility sponsors
RS6-2, Change Control Program
This reseach outlines nine suggested elements of a change control program: (RS6-2, p. 13)
- Owner Commitment to Change Control: Install a formal change review commitee
- Team effort: Among owner, engineering, and contractor
- Freesing Design: Time to freeze design is after P&IDs have been completed
- Formal Change Justification: Every change must be justified and reviewed by supervisors and affected parties. The initiaor of the change must estimate the impact of the change both as to cost and schedule, identify other areas of the project that may be affected by the change.
- Selected Change Justification
- Operating Facility Liaison
- Optional change: Some changes could provide cost savings, however it can have considerable consequential effects that overrun the saving.
- Filtering Changes form Owner Personnel
- Contractor Incentives
This research recommends 24 actions to eliminate/minimize problems associated with inadequate scope definition during the feasibility, conceptual engineering, detailed engineering and construction phases. (RS6-2, p. 17)