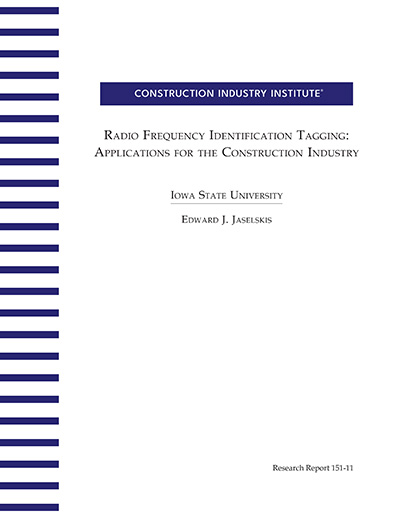
Radio Frequency Identification Tagging: Applications for the Construction Industry
This report provides construction industry owners and contractors with current information about enhancing their operations using radio frequency identification (RFID) technology. Radio frequency identification involves the use of tags, or transponders, that collect data and manage it in a portable, changeable database; communicate routing instructions and other control requirements to equipment; and withstand harsh environments. It can be viewed as a sister technology to bar code labels which use light waves instead of radio waves to read a tag. An RFID system comprises tags, or transponders, and a reader that, depending on configuration, includes an antenna and scanner. The tag contains a small integrated circuit chip and an antenna that is encapsulated in a protective shell. The reader contains, at a minimum, an antenna and scanner and is used to communicate with the tag. Tags can be categorized as read only or have both read and write capabilities. Moreover, they are classified as active, which means they include a battery, or passive, which means they are powered by the reader’s energy field. The memory capacity of the tags varies from 64 to 32,768 bytes (one byte equals eight bits of binary code). The technology, in existence for several years, is currently being used in several application areas such as vehicle access, personnel identification, asset tracking, livestock identification, and tolls and fees. Application development is currently underway in areas related to groceries, postage stamps, and baggage identification in airports.
The primary benefits of using RFID technology are its ability to store data and retrieve it at a later time. In addition, unlike bar code labels, it is more robust because RFID tags are not damaged as easily, can be read in direct sunlight, and survive harsh conditions. Limitations include higher tag costs compared to bar code labels; lack of standardization, which prohibits one manufacturer’s reader from reading another manufacturer’s tag; and potential interference from steel objects and other radio frequency signals.
The purpose of this research project was to disseminate information regarding RFID to owner and contractor organizations, enabling them to take advantage of this emerging technology as it becomes commercially available. The project report also provides RFID manufacturers with relevant information regarding the needs of the construction industry so future RFID products better address the industry’s needs.
The scope of this research project includes (1) providing Construction Industry Institute (CII) member companies with a better understanding of RFID tagging technology (what it is, how it works, benefits, costs, and current applications); (2) understanding CII member company needs in terms of what applications will best suit their needs, the type of data that should be stored on each tag, and barriers to implementation; (3) pilot-testing applications in the construction and owner facility operations environment; and (4) assessing how RF tagging technology can be incorporated into a fully integrated, automated project process (FIAPP).
A construction industry–RFID supplier workshop was held to disseminate information about this technology and to generate suitable application ideas for the industry. Thirty-one people attended the workshop, which included representation from both CII owner and contractor firms and four RFID suppliers (Brady RFID Systems, HID, Intermec-Amtec, and SAT Corporation). Potential application areas discussed by participants included material management and procurement (e.g., material receiving, installation, and startup and commissioning), field operations (e.g., personnel management, timekeeping, handling certification for mechanical machinery, and fleet management), and maintenance (e.g., inspection, repair history, operating data, and compliance records). Moreover, the following critical points were identified during the workshop:
- RFID has its strengths and limitations.
- There are few construction-related RFID suppliers.
- RFID should be used with the larger company information system (FIAPP).
- Bar code labels and RFID tags should be considered complementary technologies.
With the information gathered during the workshop, five application ideas were selected and pilot tests conducted to learn more about RFID and its applicability to the construction industry. One contractor application, related to receiving pipe supports on a jobsite, was explored. Three owner applications related to (1) tracking smart instruments, (2) maintenance of pressure relief valves, and (3) operator rounds and mechanical integrity inspections were tested on existing plant facilities. The National Institute of Standards and Technology also conducted an experiment using RFID to track steel components on a job site. These tests involved the use of passive RFID technology in the 125-KHz frequency range.
Results from these pilot tests showed that RFID can potentially reduce costs for both owners and contractors. The contractor pilot showed that RFID tags reduced the time required to download data into a company’s material tracking system and could “flag” an item so an entry was not repeated. When scanning the tags, sun glare was not a problem. Furthermore, it was perceived that there were lower rework costs, reduced inventory shrinkage, reduced start-up times, and positive material identification for the owner applications.
This report also investigates ways to integrate RFID technology throughout the project life cycle, improving productivity, cost, schedule, quality, and safety. The primary areas are related to construction (personnel accountability, safety, rigging equipment, fleet management, measuring and testing equipment, quality, and material control) and owner operations. From the owner’s perspective, asset management would provide the greatest benefit. At the point of manufacture, RFID tags could be encoded with specific information by the manufacturer that the contractor would use upon receipt for inventory control at the site, including preventive maintenance requirements that would apply throughout the component’s life and during the storage cycle of the project. When the asset was turned over to the owner, the information stored on the RFID tag could be used to track the asset’s life during its maintenance and operation period.
Radio frequency identification is becoming more popular as a tagging and identification technology. In addition to its relatively large storage capacity, it is very reliable and extremely robust in harsh environments. This technology also has a high level of security because it is nearly impossible to replicate tag information. Several applications have already been successfully developed using this technology. As demonstrated by the contractor and owner pilot tests, RFID is a promising technology for enhancing construction operations related to material receiving and also possibly other operations related to maintenance and operations. Overall, this technology has significant potential for enhancing several processes in the construction and facility operations environment.