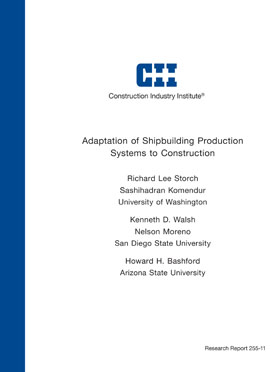
Adaptation of Shipbuilding Production Systems to Construction
During its history, the Construction Industry Institute (CII) has analyzed company practices and identified many best practices and potential best practices by which productivity could be increased. The industry is certainly in need of productivity improvement. In 1947 Fortune magazine declared that construction was the industry that “missed the industrial revolution,” and conventional wisdom holds that the industry has changed very little since the rise of a specialized workforce, more or less contemporaneous with the industrial revolution. US economic statistics indicate that construction productivity has declined. The underlying data and calculations have been called into question, but while non-farm productivity outside construction has been increasing at around a 3% per annum rate, few would argue that construction has exceeded half that rate. The dramatic increases in productivity outside construction are largely attributed to increases in mechanization and information technology – two areas in which the construction industry certainly lags. Recently, CII’s Research Team 232 reported that practices adopted by the shipbuilding industry, particularly in Asia, have resulted in dramatic improvements. Because of many similarities between construction and shipbuilding (e.g. project scale, tools and processes employed), RT 232 concluded that some of the techniques which have revolutionized shipbuilding could be adopted in the construction industry also. This project intended to consider that proposition in more detail in hopes of identifying a path to step changes in productivity.
The shipbuilding experience relied upon a number of factors to drive the successes that have been witnessed over the last several decades, but the principal enabler is a design-production integration scheme referred to by RT 232 as the “interim product database” (IPD). The IPD consists, in essence, of a library of designs for “chunks” or modules of ships, design rules to allow rapid resizing, and all of the production information to drive a mechanized, automated assembly line to construct those chunks. Tight interface tolerance and routing rules further support this production method, so that the modules produced can be confidently expected to accurately connect together. The primary value-added for this project was to be a detailed design of a production system for a case-study project in a construction setting based on an IPD, with sufficient detail to understand associated capital costs and benefits for adoption of this production scheme.
Initially, there were three specific project objectives:
- Design a production system based on an IPD approach for construction of a construction industry project. One possibility was an offshore product, such as an LNG trans-shipment and storage facility, a production platform or a similar product. Based on initial discussions with Petrobras, there was a strong likelihood that they would be interested in being involved in the case study. A second possibility was a multi-family midrise project. Initial discussions with a developer/builder in the Utah Wasatch front area who was planning to develop an IPD based facility, indicated they would be very open to working with the research group to participate in the facility development planning and allowing open access by the research group during facility start-up and during construction of the initial projects. The research group intended to contribute to the planning process by assisting in developing process maps, reviewing work station activities, and suggesting equipment and technologies for the work stations of which the developer may not be aware. The design would include a revised process flow diagram for design and construction activities, a listing of proposed assembly stations with equipment lists and ROM costs, and simulation of the system to demonstrate function, benefits, and operating costs. For the midsize building case, actual cost and performance data will be available for analysis.
- Conduct case studies of projects done in an “IPD-like” matter in construction, with detailed documentation of the actual approach, and determine what conditions blocked the adoption more broadly.
- Identify to what extent the construction affiliates of shipyards relying heavily on the IPD approach are translating that approach to construction.
Soon after the project began, the economic climate changed rapidly. The ensuing economic downturn impacted the plans of both companies that were intended to provide the detailed case study. As a result, the depth of the detailed case study needed to be reduced. In partial response to the inability to partner with a company to do a detailed case study, Chapter III was added to show how detailed design rules have been developed in shipbuilding. An increased review of mini-case studies was added and is presented in Chapter IV. Some work was completed on the Petrobras case study and is presented in Chapter VI. A similarly reduced case study of the developer/builder was conducted and is presented in Chapter V. Finally, an additional case study of a pharmaceutical manufacturing company was added and is presented in Chapter VII. Chapter VIII presents a detailed barriers analysis.
The research identifies virtually no data to substantiate the following, but there are common patterns that can be drawn from the five case studies:
- Project Cost Savings – Economic benefits will be realized as projects move from the high-risk stick-built environment to an IPD modularized approach. However cost saving are marginal or limited in research studies to-date. Productivity differentials over field conditions were observed in modular facilities due to controlled conditions, closer supervision, and easier access to tools, but very little hard data suggests cost savings are identified. The report analyzes one case study regarding the economics of building an off-site modular manufacturing facility.
- Lower Material Cost – No specific material cost savings is identified in the case studies; however the research identifies potential savings through bulk purchases and economies of scale.
- Improved Safety and Higher Quality – The prefabrication sites typically saw improved safety statistics over a site construction due to the safe, sometimes climate controlled, environment. The environment reduced hazards and improved working conditions, thus improving both safety and quality. In addition, projects requiring stringent quality construction can benefit from a modular approach due to easy off-site verification of quality standards.
- Single Project Focus Impedes Modular Investment – The case studies identified the limited re-use of designs in the development of a core module library do to the specific design function of each project.